Defiant Electronic Deadbolt Troubleshooting
Most troubleshooting will be performed when you have completed the wiring and try to use the system or on a service call, where you have to determine why the door is not locking of unlocking.
- Defiant Electronic Deadbolt Reset Code
- Defiant Electronic Deadbolt Programming Instructions
- Defiant Electronic Deadbolt Troubleshooting Video
Electric locks are both mechanical as well as electrical. The physical element of the device does the locking and the electrical element controls the clocking or unlocking.
Problems with the SmartCode are most often caused by improper door alignment or missed programming procedures. Step 1 Take the battery pack out of the unit and depress the button labeled 'Program' three times if the unit doesn't operate properly after installation or fails to open with a key. The good choice of a Best Defiant Electronic Deadbolt Troubleshooting depends on the convenience of use and much other stuff. We have passed our entire journey of shopping, including reviews and online research; so we know the whole online shopping process is working in many different ways. Defiant Electronic Deadbolt User Manual Other brands that indent ring an is only option that you don't have to use. Maybe someone installing didn't put hole in right place, if it's too far off the lock when flush may expose the hole some.
Electric locks are either failsafe (normally power is applied to maintain locked condition; when power is removed the lock releases) or fail secure (no power applied the device is locked; when power is applied, the device unlocks).
For diagnostic purposes, electric locking systems can be divided into three sections:
Power Source
Logical Control and Wiring
The Locking Device
When a call comes in for the troubleshooting of an electric locking system, I always hope that whoever took the call bothered to gather some information about the project.
Too many times the technician will call in to report that he went over the door locking system with a magnifying glass, but was unable to find anything wrong. Then you find out he was looking at the wrong door.
Some companies keep a record of installations. Some companies put qualified personnel on the phone to take information from callers. Some don’t.
We have a couple of folks in our company who won’t tell you anything. You are lucky to obtain the address of the client, much less information on who did the installation, when it was installed (in or out of warranty?), what door it is, the nature of the malfunction, the kind of equipment that is installed on the door, and who the tech should speak to on site.
Not obtaining adequate information beforehand almost guarantees it will require more than one trip to the site to complete the repair.
So the first item you will need to troubleshoot a locking system is INFORMATION. Ask the following questions:
Was the system properly designed/installed in the first place?
Is there power (to the lock)?
Is there physical damage to the lock or door assembly?
Is the access control system working properly?
Once on site, you need to locate your contact person and confirm the door you are supposed to be repairing and the malfunction.
Your customer may be a terrific person and a highly valuable member of society, but not able to articulate the issue they are experiencing with the system. A physical inspection of the door and components would be an excellent starting point.
Loose door hardware, defective door closers or worn hinges can all be reasons for the door to not be working as expected, and looking the door over is quick and easy. Remember that an exit door which does not latch, or freely swing open from the inside to permit egress is considered and obstructed exit, and is a life safety hazard. State clearly on your service ticket that a life safety issue exists which needs immediate attention.
Once you’ve determined the door is not a death trap, you can continue troubleshooting.
Is there power to the lock or to the system? Sometimes the power supply is a wall wart type that someone has kicked loose, or it has been unplugged so someone could use a vacuum cleaner or corn popper in the receptacle.
Another cutie is the receptacle being used for the power supply is on a wall switch, producing mystical symptoms. A loose wire on the power supply is also possible especially if the wall wart has been swinging on the wire.
Often when locking systems are deployed, the power supply is inside a metal enclosure which uses a line cord for line voltage. We often do this to avoid having to get an electrician to hard-wire the power supply. Hard-wiring is when an electrician makes a permanent connection of the line voltage input of the power supply to an existing or new branch circuit in the structure. The electrician should verify that if it an existing branch circuit that the total load does not exceed that rating of the wiring or circuit breaker. Depending on the lock and the environment in which the lock is being installed, the nature of the other equipment on the circuit may be relevant to the proper operation of the lock or the door/access control.
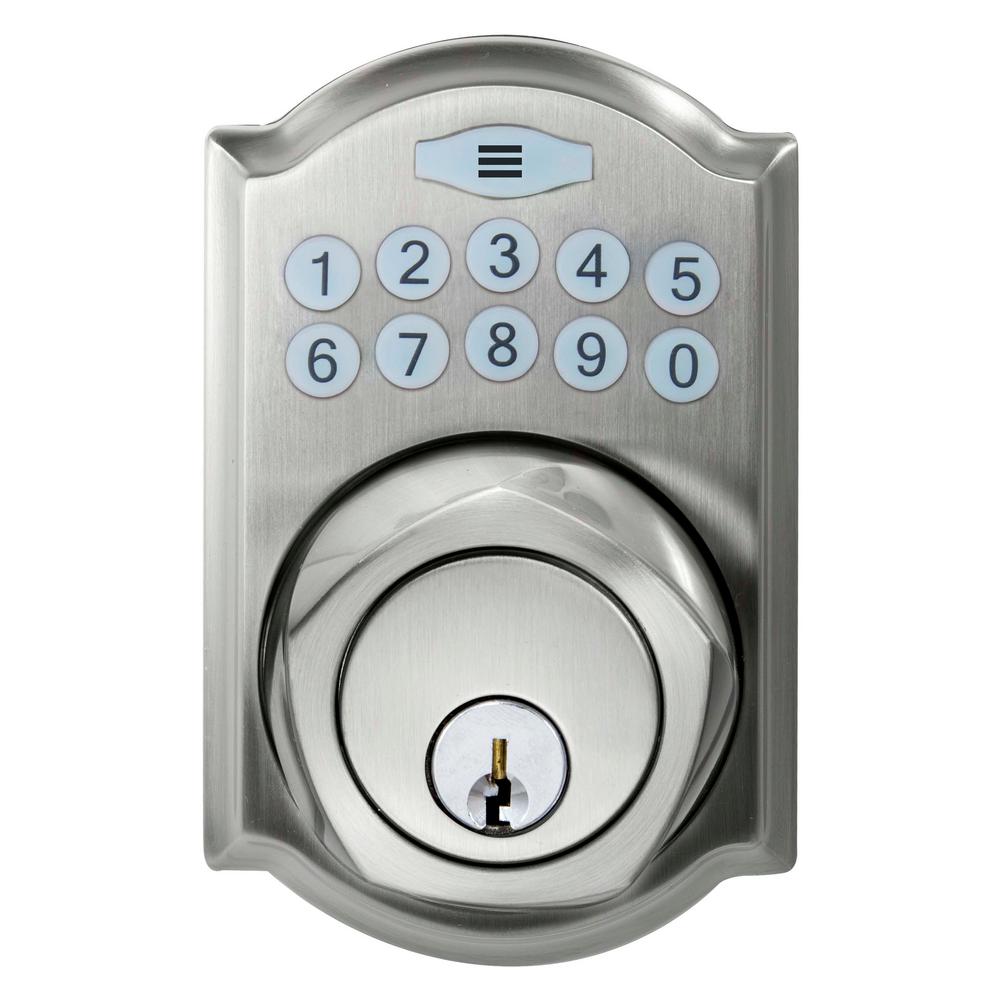
The electrician should also clearly identify the location and ID# of the breaker (Panel AA; Breaker #14 doesn’t always tell you enough for you to locate it).
Having testers helps. I use a few different types including a Digital Multimeter, and some toners, a CAT5/Coaxial cable tester I got off e-Bay for $10 and a Fluke cable checker which serves as a tone generator and cable integrity tester.
I learned long ago that beginning my service call by metering everything is a waste of time. But I do use my meter skillfully and frequently; and it never ceases to amaze me when I ask a tech if he has a meter with him, or if he measured voltage, and the answer is ‘no’.
Except for sparks, heat and smoke and possibly a tingle here and there, you cannot sense Voltage, you need a meter. The Internet abounds with tutorials on how to use a meter and advice about how much you should invest in a meter.
I require accuracy, reliability, durability, an easy to read display, and the ability to measure AC/DC Voltage, resistance, audible continuity, and current. I appreciate a meter that can withstand being dropped off a ladder, and one which has abundant electrical insulation to protect me from electrical shock. I am willing to pay a little more for a good the right tools for the job.
You can check a receptacle with a meter or a voltage tester which does not require you to physically touch conductors or stick things in a receptacle.
If the lock is on a timer control, check that. Some timers run on line voltage and if there is a power outage, they resume working when power is restored, only they will be no longer set to the correct time of day. So the doors won’t unlock or relock when they are expected to.
Some timers have their own integral battery backup, and will continue to keep accurate time during a power failure.
If the system is uses credentials or PINs (personal identification numbers), you can try to see if the lock works by actuating a REX (request to exit) or remote door release button if there is one being used. Bypassing the reader or keypad may reveal the issue is with the Electronic Access Control rather than the locking device.
All these steps are in an attempt to isolate the source of the problem.
Perhaps there is not enough voltage reaching the locking device. Does the electric lock buzz weakly instead of click authoritively? Measure the voltage at the power supply and compare that reading to the voltage across the electric lock when the power is applied. This works for both failsafe or fail secure locks. Sony kdl32ex550 bravia hdtv firmware 1.402gaa for mac. Low voltage will prevent both failsafe as well as fail secure locks from behaving.
If a maglock is not locking, it could be related to the voltage being applied to the lock, the alignment between the armature and the coil, or of course the controller.
If the maglock will not release, it indicates two problems. First, a failure in the controlling circuit is preventing power from being interrupted to the daglock. It could be a shorted wire in a power transfer, or some other failed device
The second problem is that the system is not designed correctly, because any electromagnetic locking system should have redundant means of forcing the electromagnetic lock to unlock for free (safe) egress.
With electric strikes, often the latch loading against the gate of the strike will prevent it from releasing. You can determine if this is the issue by applying pressure on the door so the lock latch is not pushing against the strike gate, and then actuating the electric lock. If it works properly under this test, you need to adjust the door so the pressure is eliminated.
A warped door will cause the problems. Bad hinges can also cause this symptom. A weak or poorly adjusted door closer which is not pulling (or pushing the door in the latch position can allow this problem to occur. A defective door closer which does not control the swing of the door can also lead to the destruction of the door release due to the impact of the door slamming into the frame.
The door may have ‘dropped’ due to wear to a pivot or hinge, and the latch is hitting on the strike frame. Wear marks will indicate if this condition exists. Any binding between the door, the door lock and the strike will cause problems.
Shear locks combine the power of an electromagnet with the strength of a mechanical interlock to produce a locking solution which can be used on bi-swinging doors. Amar chitra katha torrent. The electrified portion of the lock is mounted on the door frame, and the armature is mounted on the door. Most often the shear lock is mounted horizontally so when power is applied the armature is pulled up to the electromagnet. Therefore gravity works for releasing the lock, and against relocking it.
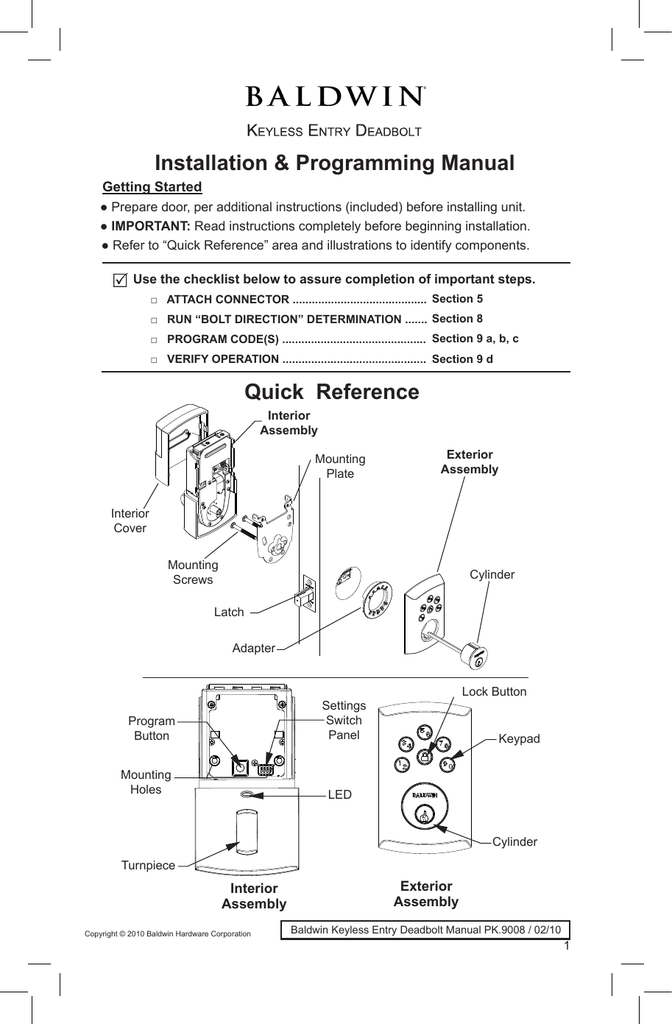
Initial adjustment of the shear lock is performed with the door aligned (zeroed) in the frame, and the height of the door at a particular point. Once the shear lock is in service, the door may eventually fail to close to the zero position, or it may wear on the pivots or hinges, and the gap between the armature and the electromagnet will increase. The result will be the shear lock will not operate as intended; the armature will not interlock with the electromagnet or the power of the electromagnet will not be sufficient to overcome the increased gap between it and the armature and the magnetic bond will not happen or it will be less than intended.
Electric bolts were once used extensively in door control. As with shear locks, alignment is critical for these to lock and unlock properly. The failure to lock is a security issue. The failure to unlock is a safety issue.
I still remember the very long Friday evening I spent carving up the door header brick, and plaster on an ornate lobby door when the electric bolt froze up in the locked position.
Besides the potential for an internal failure in an electric bolt, they may also be subjected to excessive side pressure from pedestrians ploughing into the locked door.
Defiant Electronic Deadbolt Reset Code
I have read in reliable industry reports that electric bolts have been outlawed in certain jurisdictions and if you encounter a defective one, to not simply install another one or repair it, but rather provide an alternative locking solution.

Defiant Electronic Deadbolt Programming Instructions
There are some quality electric bolts on the market, and in my market, electric bolts are not forbidden. Check with your AHJ, and be especially astute when you encounter an electric bolt, especially a defective one.
Defiant Electronic Deadbolt Troubleshooting Video
All security troubleshooting is as much an art as it is a skill. Experience is the best teacher, so my advice is for you to hurry up and get started